Master Model CASTING |
|
|
- The number of S.L.A, (Stereolithography), Machined and Carved Master Models being produced continues to increase. Gold Star Omega+ is a new investment powder able to withstand the challenges of pattern expansion, and higher than usual burnout temperatures, to remove all of the carbon residues.
- Tests using patterns produced by a number of different companies including Envisiontec, 3D Systems, Solid Scape and Invision, cast using Omega+ have seen exceptional quality castings in terms of surface finish and faithful reproduction of the finest detail.
|
|
|
The Burnout Process |
|
|
To achieve the optimum casting results, having taken care of your Master Models, it is also important to follow the suggested burnout cycle detailed below. This cycle has been tested in the Gold Star laboratories and will help produce optimum results. It is suggested that furnaces are calibrated for temperature control regularly. |
|
|
Taking Care of Master Models |
|
There are some important rules to follow when producing Master Models for casting and these should be followed so that the best quality casting is achieved. |
|
• Waxes and Resins should be stored at the correct temperature as suggested by the supplier.
• After production, resin patterns should be cleaned and allowed to dry before being stored in an
airtight container with a silicon absorption pad.
• The patterns should then be placed into a sealed container with a silicon gel bag.
• Patterns must not be taken out of the sealed container or excessively handled until ready for
spruing. |
|
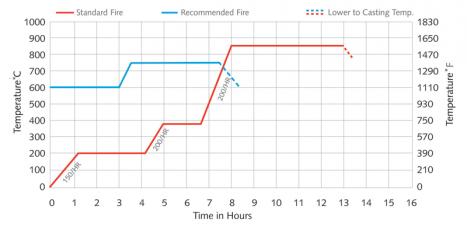 |